アルミ材に対するプレス技術と溶接技術の融合
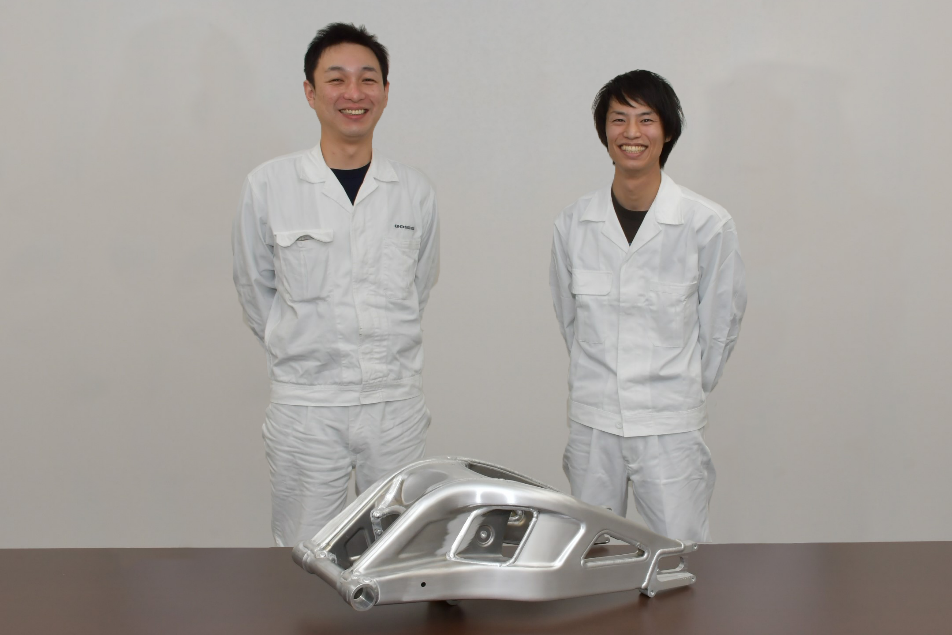
アルミ材に対する
プレス技術と溶接技術の融合
技術BL
合志 亮祐 / 中嶋 竜一
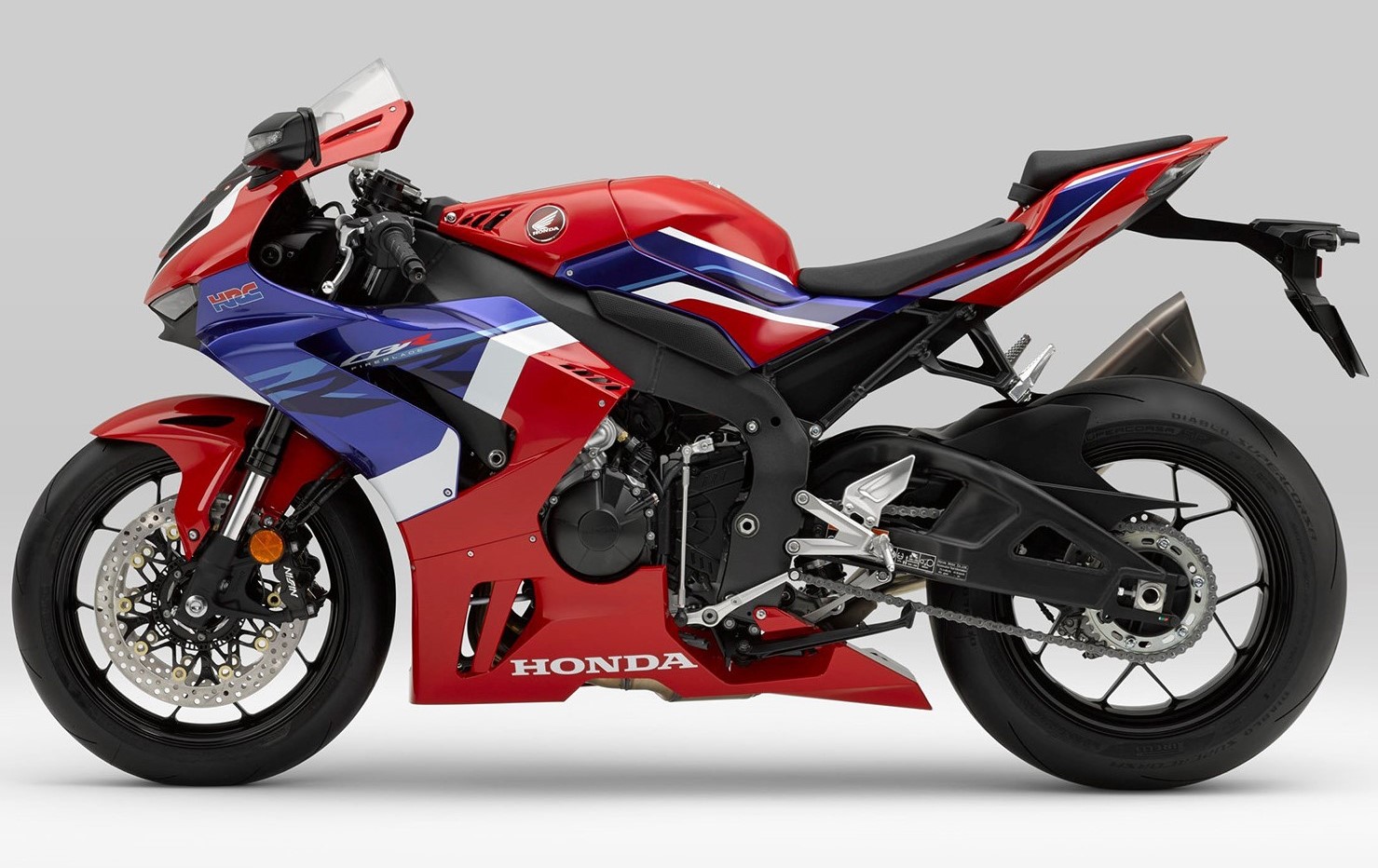
アルミ材に対する
プレス技術と溶接技術の融合
GPマシンと同様のプレスフォーミングスイングアームにより剛性バランスを追及し、複数のアルミ板を溶接する製造手法。
CBR1000RR
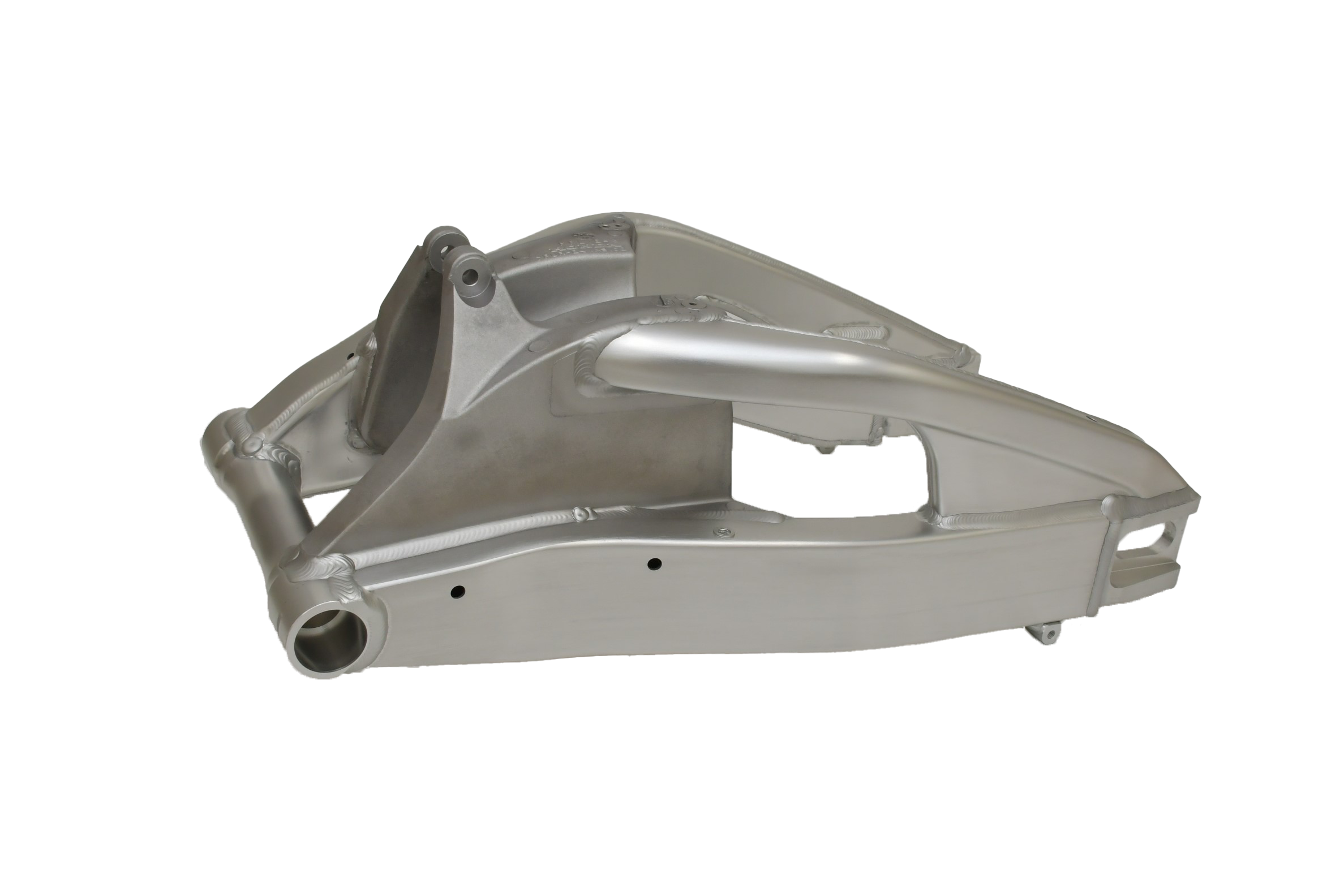
CBR1000RR-R
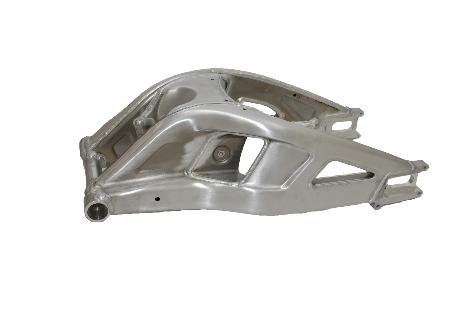
プレス深絞り成形
今回のスイングアームはアルミ板の成形部品を中心に構成されていました。
アルミ部品成形の経験が殆どないうえに、部品形状の凹凸が大きく、成形ができるか分からない状況でスタートしました。
案の定、試作品の製作時は問題が多発しました。
一つ一つの問題点をシュミレーション検証と試作製作を何度も繰り返すことで解決していき、無事に量産化につなげることができました。
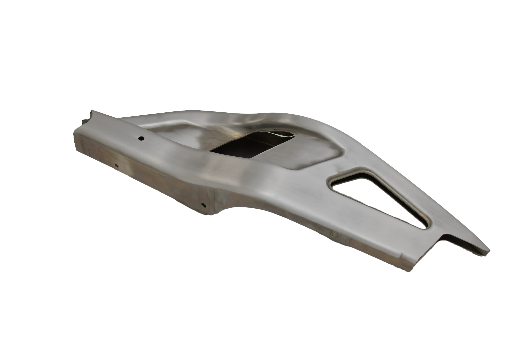
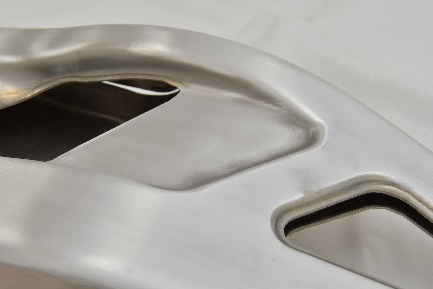
溶接技術
旧モデル溶接長(5900mm)に対し新モデル溶接長(9800mm)
パーツ18部品を組み合わせる技術難易度が高い製品です。
溶接ビードが長く熱影響を如何に抑えるかが課題でした。
溶接職人の技術を自動化に活かし、溶接歪を抑える工夫を治具に採用しました。
その結果、溶接自動化率100%により品質の均一化が達成できました。
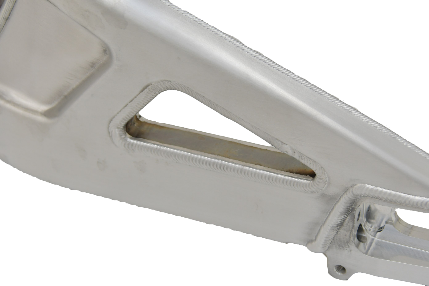
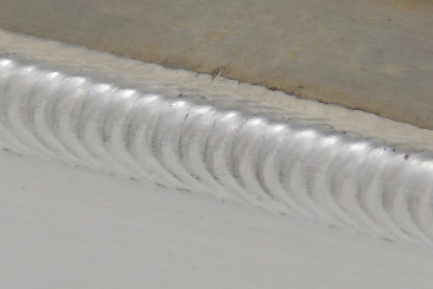